Korozyon oranı, hem dış çevre koşullarına hem de malzemenin iç özelliklerine bağlı olan çok faktörlü bir parametredir. Normatif ve teknik belgelerde, ekipmanın ve bina yapılarının çalışması sırasında sorunsuz çalışmasını sağlamak için izin verilen metal tahribatı değerleri üzerinde belirli kısıtlamalar vardır. Mühendislikte korozyon oranını belirlemek için evrensel bir yöntem yoktur. Bu, tüm faktörleri dikkate almanın karmaşıklığından kaynaklanmaktadır. En güvenilir yöntem tesisin işletme geçmişini incelemektir.
Kriter
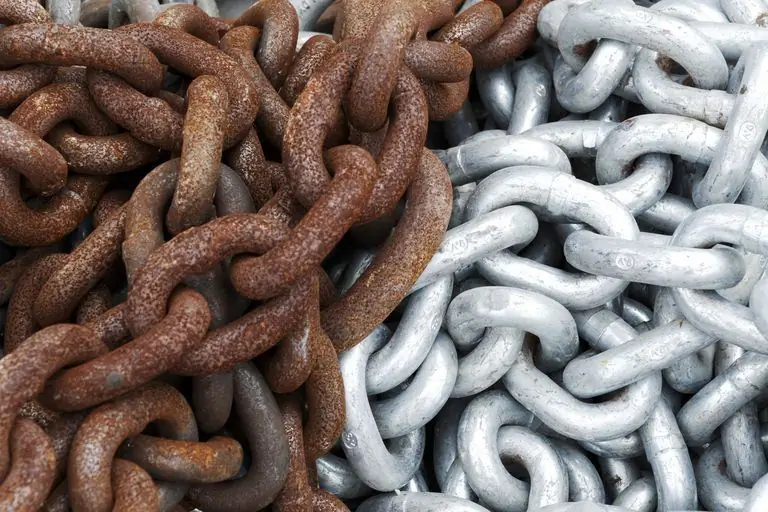
Şu anda mühendislik tasarımında birkaç korozyon hızı kullanılmaktadır:
- Doğrudan değerlendirme yöntemine göre: birim yüzey başına metal parçanın kütlesindeki azalma - ağırlık göstergesi (1 saat boyunca 1 m'de gram olarak ölçülür2); hasar derinliği (veya korozyon süreci geçirgenliği), mm/yıl; korozyon ürünlerinin salınan gaz fazının miktarı; ilk korozyon hasarının ortaya çıktığı süre; birim alan başına korozyon merkezi sayısıbelirli bir süre boyunca ortaya çıkan yüzeyler.
- Dolaylı tahmin: elektrokimyasal korozyon akımı gücü; elektrik direnci; fiziksel ve mekanik özelliklerde değişiklik.
İlk doğrudan değerleme göstergesi en yaygın olanıdır.
Hesaplama formülleri
Genel durumda, metalin korozyon hızını belirleyen ağırlık kaybı aşağıdaki formülle bulunur:
Vkp=q/(St), burada q metalin kütlesindeki azalmadır, g;
S - malzemenin aktarıldığı yüzey alanı, m2;
t - zaman aralığı, saat
Sac levha ve ondan yapılan kabuklar için derinlik indeksini (mm/yıl) belirleyin:
H=m/t, m metale nüfuz etme derinliğidir.
Yukarıda açıklanan birinci ve ikinci göstergeler arasında şu ilişki vardır:
H=8, 76Vkp/ρ, burada ρ malzemenin yoğunluğudur.
Korozyon hızını etkileyen ana faktörler
Aşağıdaki faktör grupları metal imha oranını etkiler:
- iç, malzemenin fiziksel ve kimyasal yapısıyla ilgili (faz yapısı, kimyasal bileşim, parçanın yüzey pürüzlülüğü, malzemedeki artık ve çalışma gerilmeleri ve diğerleri);
- dış (çevresel koşullar, aşındırıcı bir ortamın hareket hızı, sıcaklık, atmosferin bileşimi, önleyici veya uyarıcıların varlığı ve diğerleri);
- mekanik (korozyon çatlaklarının gelişimi, döngüsel yüklerin etkisi altında metalin yok edilmesi,kavitasyon ve aşındırıcı korozyon);
- tasarım özellikleri (metal kalitesi seçimi, parçalar arasındaki boşluklar, pürüzlülük gereksinimleri).
Fiziksel ve kimyasal özellikler
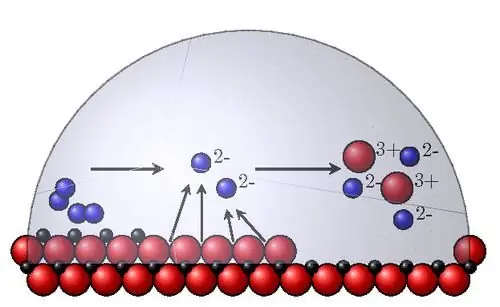
En önemli dahili korozyon faktörleri şunlardır:
- Termodinamik kararlılık. Bunu sulu çözeltilerde belirlemek için, ortamın pH'ının çizildiği apsis ekseni boyunca ve ordinat ekseni boyunca redoks potansiyeli boyunca referans Pourbaix diyagramları kullanılır. Pozitif yönde potansiyel bir kayma, malzemenin daha fazla stabilitesi anlamına gelir. Geçici olarak, metalin normal denge potansiyeli olarak tanımlanır. Gerçekte, malzemeler farklı oranlarda korozyona uğrar.
- Bir atomun kimyasal elementlerin periyodik tablosundaki konumu. Korozyona en duyarlı metaller alkali ve toprak alkali metallerdir. Atom numarası arttıkça korozyon hızı azalır.
- Kristal yapı. Yıkım üzerinde belirsiz bir etkisi vardır. İri taneli yapının kendisi korozyonda bir artışa yol açmaz, ancak tane sınırlarının taneler arası seçici yıkımının gelişimi için uygundur. Homojen bir faz dağılımına sahip metaller ve alaşımlar eşit şekilde korozyona uğrarken, homojen olmayan dağılıma sahip olanlar odak mekanizmasına göre korozyona uğrarlar. Fazların karşılıklı düzenlenmesi, agresif bir ortamda anot ve katodun işlevini yerine getirir.
- Kristal kafesteki atomların enerji homojensizliği. En yüksek enerjiye sahip atomlar yüzlerin köşelerinde bulunur.mikro pürüzler ve kimyasal korozyon sırasında aktif çözünme merkezleridir. Bu nedenle metal parçaların dikkatli bir şekilde işlenmesi (taşlama, cilalama, finisaj) korozyon direncini artırır. Bu etki aynı zamanda pürüzsüz yüzeylerde daha yoğun ve daha sürekli oksit filmlerinin oluşmasıyla da açıklanmaktadır.
Orta asitliğin etkisi
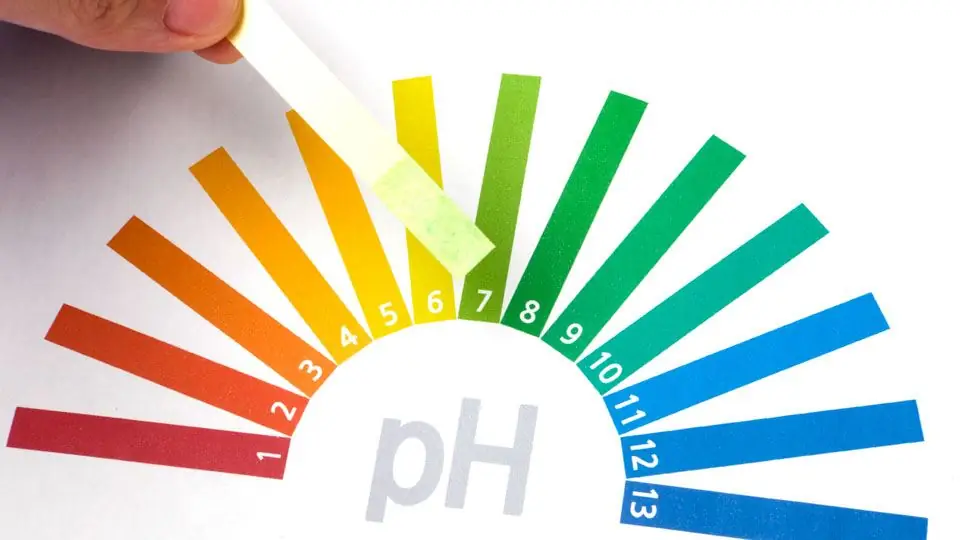
Kimyasal korozyon sürecinde, hidrojen iyonlarının konsantrasyonu aşağıdaki noktaları etkiler:
- korozyon ürünlerinin çözünürlüğü;
- koruyucu oksit filmlerinin oluşumu;
- metal imha oranı.
PH 4-10 birim (asidik çözelti) aralığında olduğunda, demirin korozyonu nesnenin yüzeyine oksijen penetrasyonunun yoğunluğuna bağlıdır. Alkali çözeltilerde korozyon hızı önce yüzey pasivasyonu nedeniyle azalır, daha sonra pH >13'te koruyucu oksit filmin çözünmesi sonucu artar.
Her metal türü için, çözeltinin asitliğine bağlı olarak yıkım yoğunluğunun kendi bağımlılığı vardır. Asil metaller (Pt, Ag, Au) asidik ortamda korozyona dayanıklıdır. Zn, Al hem asitlerde hem de alkalilerde hızla yok edilir. Ni ve Cd alkalilere karşı dayanıklıdır ancak asitlerde kolayca korozyona uğrar.
Nötr çözeltilerin bileşimi ve konsantrasyonu
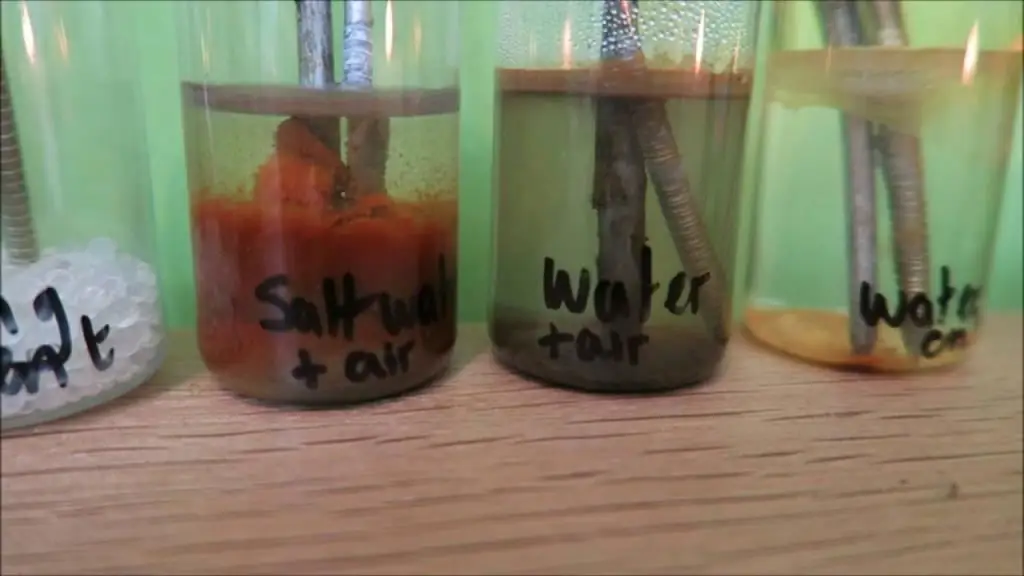
Nötr çözeltilerdeki korozyon hızı daha çok tuzun özelliklerine ve konsantrasyonuna bağlıdır:
- Tuzların hidrolizi sırasındaaşındırıcı bir ortamda, metal tahribatının etkinleştiricileri veya geciktiricileri (inhibitörleri) olarak işlev gören iyonlar oluşur.
- PH'ı artıran bileşikler aynı zamanda yıkıcı işlemin hızını da arttırır (örneğin soda külü) ve asitliği az altanlar onu az altır (amonyum klorür).
- Çözeltide klorür ve sülfatların varlığında, belirli bir tuz konsantrasyonuna ulaşılana kadar (klorür ve kükürt iyonlarının etkisi altında anot işleminin yoğunlaştırılmasıyla açıklanır) yıkım aktive edilir ve daha sonra oksijenin çözünürlüğündeki azalma nedeniyle kademeli olarak azalır.
Bazı tuz türleri, çözünmeyen bir film oluşturabilir (örneğin, demir fosfat). Bu, metalin daha fazla tahribattan korunmasına yardımcı olur. Bu özellik pas nötrleştiricileri uygularken kullanılır.
Korozyon önleyiciler
Korozyon önleyiciler (veya önleyiciler) redoks işlemi üzerindeki etki mekanizmalarında farklılık gösterir:
- Anot. Onlar sayesinde pasif bir film oluşur. Bu grup, kromatlar ve bikromatlar, nitratlar ve nitritlere dayalı bileşikleri içerir. Son tip inhibitörler, parçaların interoperasyonel koruması için kullanılır. Anodik korozyon önleyicileri kullanırken, küçük miktarlarda eklenmesi tahribat oranında bir artışa yol açabileceğinden, öncelikle minimum koruyucu konsantrasyonlarını belirlemek gerekir.
- Katot. Eylemlerinin mekanizması, oksijen konsantrasyonundaki bir azalmaya ve buna bağlı olarak katodik süreçteki yavaşlamaya dayanır.
- Koruma. Bu inhibitörler, koruyucu bir tabaka olarak biriken çözünmeyen bileşikler oluşturarak metal yüzeyi izole eder.
Son grup, oksitleri temizlemek için de kullanılan pas nötrleştiricileri içerir. Genellikle fosforik asit içerirler. Etkisi altında, metal fosfatlama meydana gelir - güçlü bir koruyucu çözünmeyen fosfat tabakasının oluşumu. Nötrleştiriciler bir püskürtme tabancası veya rulo ile uygulanır. 25-30 dakika sonra yüzey beyaz-gri bir renk alır. Kompozisyon kuruduktan sonra boya ve vernikler uygulanır.
Mekanik hareket
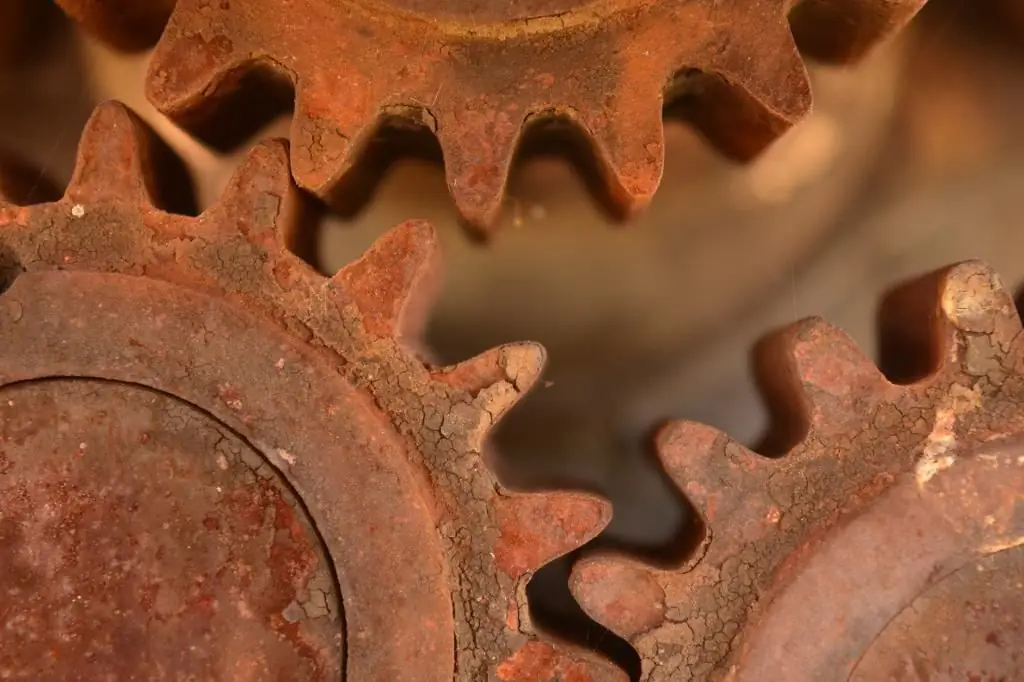
Agresif bir ortamda korozyonun artması şu tür mekanik işlemlerle kolaylaştırılır:
- İç (kalıplama veya ısıl işlem sırasında) ve dış (harici uygulanan bir yükün etkisi altında) gerilmeler. Bunun sonucunda elektrokimyasal homojensizlik oluşur, malzemenin termodinamik kararlılığı azalır ve korozyon çatlaması oluşur. Oksitleyici anyonların, örneğin NaCl'nin varlığında, çekme yükleri (dik düzlemlerde çatlaklar oluşur) altında yıkım özellikle hızlıdır. Bu tür bir tahribata maruz kalan cihazların tipik bir örneği, buhar kazanlarının parçalarıdır.
- Alternatif dinamik hareket, titreşim (korozyon yorgunluğu). Yorulma sınırında yoğun bir azalma var, daha sonra büyük bir tanede birleşen çoklu mikro çatlaklar oluşuyor. Sayıbaşarısızlık döngüleri büyük ölçüde metallerin ve alaşımların kimyasal ve faz bileşimine bağlıdır. Pompa aksları, yaylar, türbin kanatları ve diğer ekipmanlar bu tür korozyona maruz kalır.
- Parçaların sürtünmesi. Hızlı korozyon, parça yüzeyindeki koruyucu filmlerin mekanik aşınması ve çevre ile kimyasal etkileşimden kaynaklanır. Sıvıda, imha hızı havaya göre daha düşüktür.
- Kavitasyon etkisi. Kavitasyon, çöken ve titreşimli bir etki yaratan vakum kabarcıklarının oluşması sonucu sıvı akışının sürekliliği ihlal edildiğinde meydana gelir. Sonuç olarak, yerel nitelikte derin bir hasar meydana gelir. Bu tür korozyon genellikle kimyasal aparatlarda görülür.
Tasarım Faktörleri
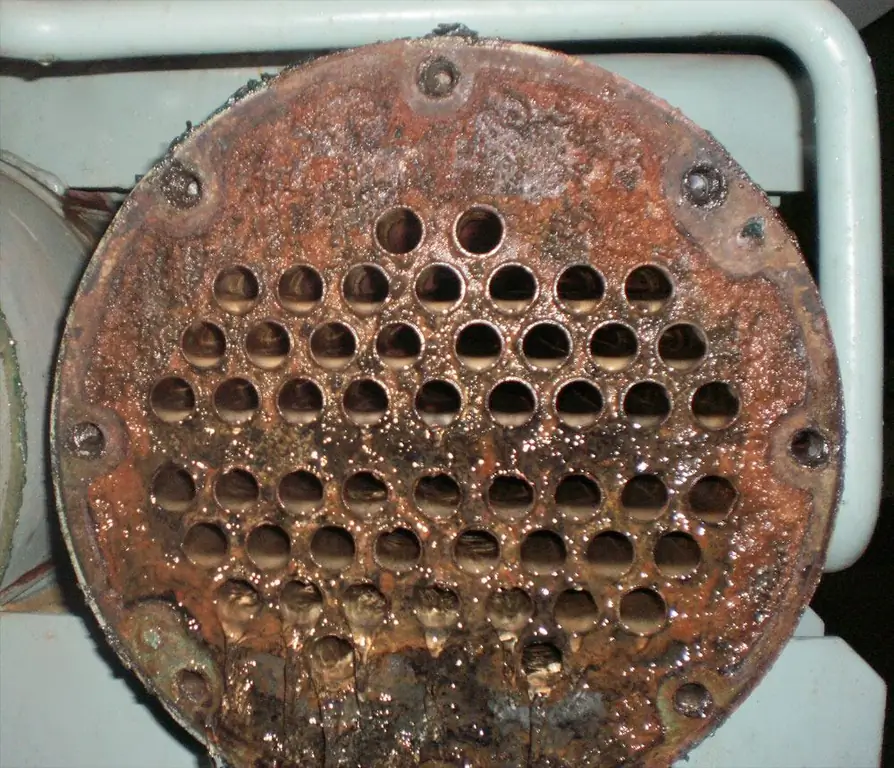
Agresif koşullarda çalışan elemanlar tasarlanırken, aşağıdaki durumlarda korozyon hızının arttığı dikkate alınmalıdır:
- Benzersiz metaller temas ettiğinde (aralarındaki elektrot potansiyeli ne kadar büyük olursa, elektrokimyasal yıkım sürecinin akım gücü o kadar yüksek olur);
- mekanik stres yoğunlaştırıcıların (oluklar, oluklar, delikler ve diğerleri) varlığında;
- işlenmiş yüzeyin düşük temizliği ile, çünkü bu yerel kısa devre galvanik çiftlere neden olur;
- Aparatın ayrı parçalarının sıcaklığında önemli bir farkla (termal galvanik hücreler oluşur);
- durgun bölgelerin (yuvalar, boşluklar) varlığında;
- oluştururkenözellikle kaynaklı bağlantılarda artık gerilmeler (bunları ortadan kaldırmak için ısıl işlem - tavlama sağlamak gerekir).
Değerlendirme yöntemleri
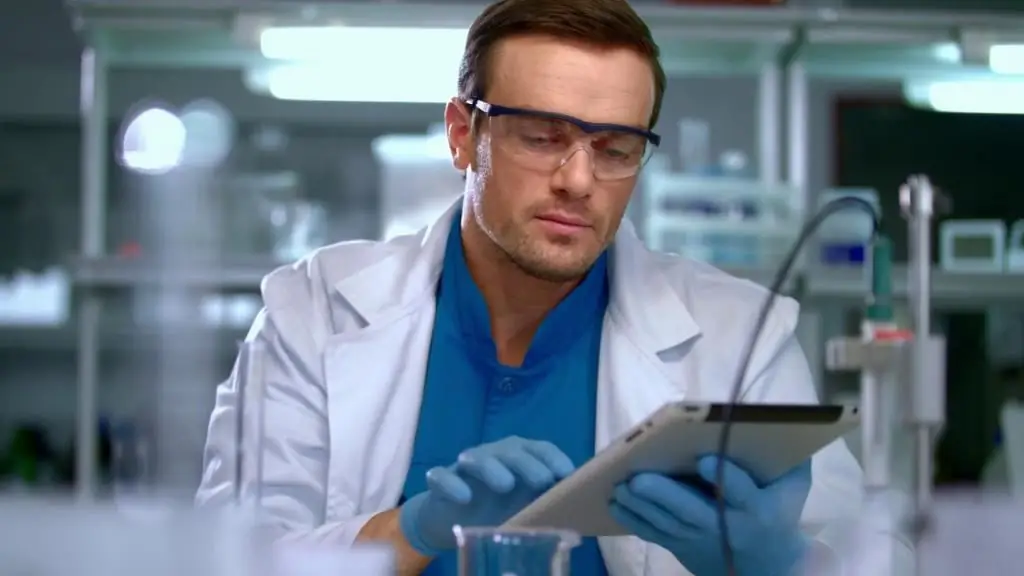
Agresif ortamlarda metallerin yok olma oranını değerlendirmenin birkaç yolu vardır:
- Laboratuvar - numuneleri gerçeğe yakın yapay olarak simüle edilmiş koşullarda test etme. Avantajları, çalışma süresini kıs altmanıza izin vermeleridir.
- Tarla - doğal koşullarda tutulur. Uzun zaman alırlar. Bu yöntemin avantajı, daha sonraki çalışma koşullarında metalin özellikleri hakkında bilgi elde etmektir.
- Doğal ortamda bitmiş metal nesnelerin yerinde testi.