Kokun yüksek fırın sürecindeki rolünden bahsedelim. Gelin bu metalurjik üretimin özüne daha yakından bakalım.
Günümüzde demir ve çelik, fırının önemli bir bileşen olduğu yüksek fırın işlemi kullanılarak yapılmaktadır.
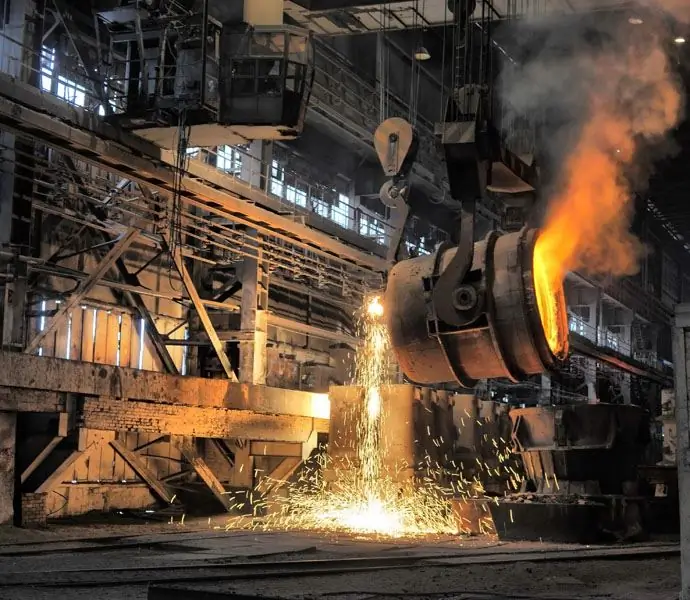
Birim özellikleri
Cihazın özelliklerini, amacını düşünün. Yüksek fırının ana süreçleri kok ergitme ile ilişkilidir. Atmosferik oksijen olmadan kömürün kalsine edilmesiyle elde edilen bir karbon kütlesinden sinterlenen gözenekli bir malzemedir.
Bir yüksek fırın, önemli miktarda patlama ve şarjın tüketildiği güçlü ve yüksek performanslı bir ünitedir.
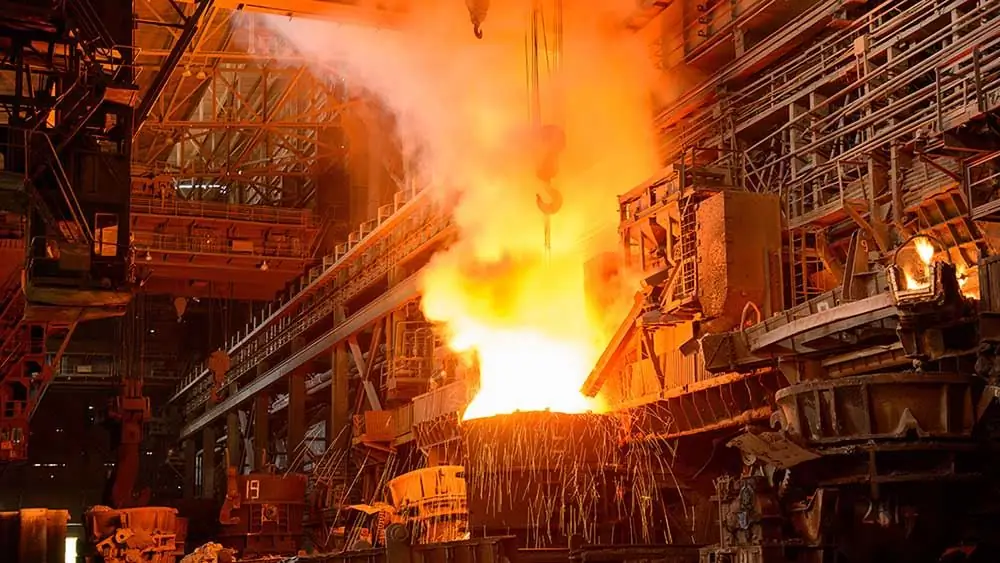
Hammadde yükleme
Modern yüksek fırın, malzemelerin 4-6 saat, gaz halindeki maddelerin 3-12 saniye içinde kalmasını gerektirir. Gazlar kesit üzerinde tamamen dağılmışsafırınlarda, yüksek erime oranlarına güvenebilirsiniz, demir üretimi devam ediyor. Yüksek fırın süreci, gazların daha düşük şarj direncine sahip bölgelerdeki hareketini hesaba katmayı içerir. Bu nedenle, fırına yüklendiğinde, ayar yapılır, kok ve sinter fırının kesiti üzerinde gaz geçirgenliği farklı olacak şekilde yeniden dağıtılır. Aksi takdirde, daha büyük bir gaz yüzdesi fırını önemli bir sıcaklıkla terk edecek ve bu da termal enerjinin kullanımını olumsuz etkileyecek, yüksek fırın süreci tam olarak verimli olmayacaktır.
Dayanıklılığı yüksek olan alanlarda gaz karışımı hafif ısıtılmış olarak geçecek, fırının alt kısmında ek ısı gerekecektir, bunun sonucunda hammadde tüketimi önemli ölçüde artacaktır.
İndirirken dikkate alınması gereken diğer özellikler nelerdir? Pik demir üretimi için yüksek fırın süreci, enerji yoğun bir üretimdir. Bu nedenle, fırının duvarlarının yakınında daha az gaz geçirgen bir aglomera tabakası kullanılır ve gaz akışının merkeze yeniden dağıtılması nedeniyle merkezde bir kok tabakası artar. Malzemeler çevre boyunca eşit aralıklarla yerleştirilmiştir.
Yük, ayrı kısımlarda yüklenir - beslemeler. Bir kısım birkaç atlama, cevher kısmı (aglomera), koktan oluşur. Orijinal bileşenlerin oranı uzmanlar tarafından belirlenir.
Yüksek fırın süreci, kok ve sinter atlamalarının büyük bir koni üzerinde toplandığı ve daha sonra bir fırına yüklendiği hammaddelerin birlikte beslenmesine olanak tanır.
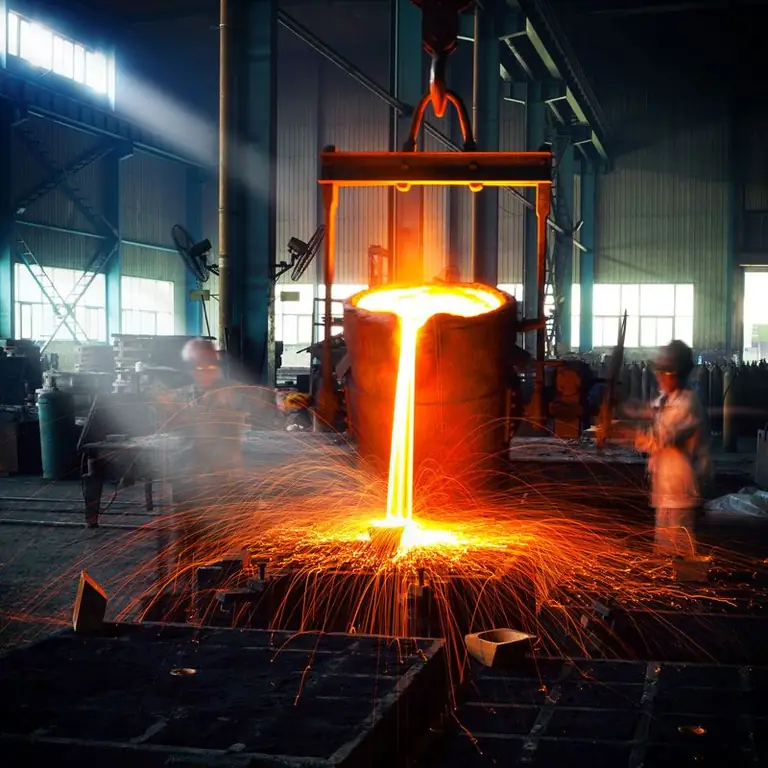
Toplu dağıtım ayarı
Kok ve aglomeratın üst kısımların enine kesiti üzerindeki dağılımı aşağıdaki yöntemlerle kontrol edilir:
- büyük koni üzerindeki hammaddelerin sırasını değiştirme;
- bölünmüş ve bölünmüş servisler geçerlidir;
- hareketli plakalar üst duvarların yakınına kurulur.
Yüksek fırın süreci, dökme malzemelerin girişi için belirli düzenliliklerin dikkate alınmasını içerir:
- büyük bir koniden düşen hammaddelerin yüksek bir tepeye döşenmesi - bir tarak;
- Yükün tepesinde (düşme noktasında) para cezaları birikir, büyük parçalar tepenin dibine yuvarlanır, bu nedenle bu bölgede yükün gaz geçirgenliği daha fazladır;
- kret, üstteki dolgu seviyesinin yanı sıra büyük bir koni ile mesafeden etkilenir;
- büyük koni tamamen inmez, bu nedenle küçük kok parçaları çevreye ulaşır.
Çoğunlukla fırının merkezi, büyük koniye en son yüklenen besleme atlamalarından malzeme alır. Yükleme sırasını değiştirirseniz, malzemelerin üst kısmın enine kesiti boyunca yeniden dağıtılmasını sağlayabilirsiniz.
Kullanılan yükün fırının hacmine dağıtım sürecini kontrol etmek için iki koni aparatı kullanılır. Son zamanlarda, bazı yüksek fırınlar, eğim açısını değiştirmenize, yatay bir düzlem boyunca hareket ettirmenize olanak tanıyan, üst duvarların yakınında hareketli plakalarla donatılmıştır.
Plakaların üzerine düşen yükün parçaları onlardan yansır, bu da ham maddeyi tepenin belirli bölgelerine yönlendirmenizi sağlar.
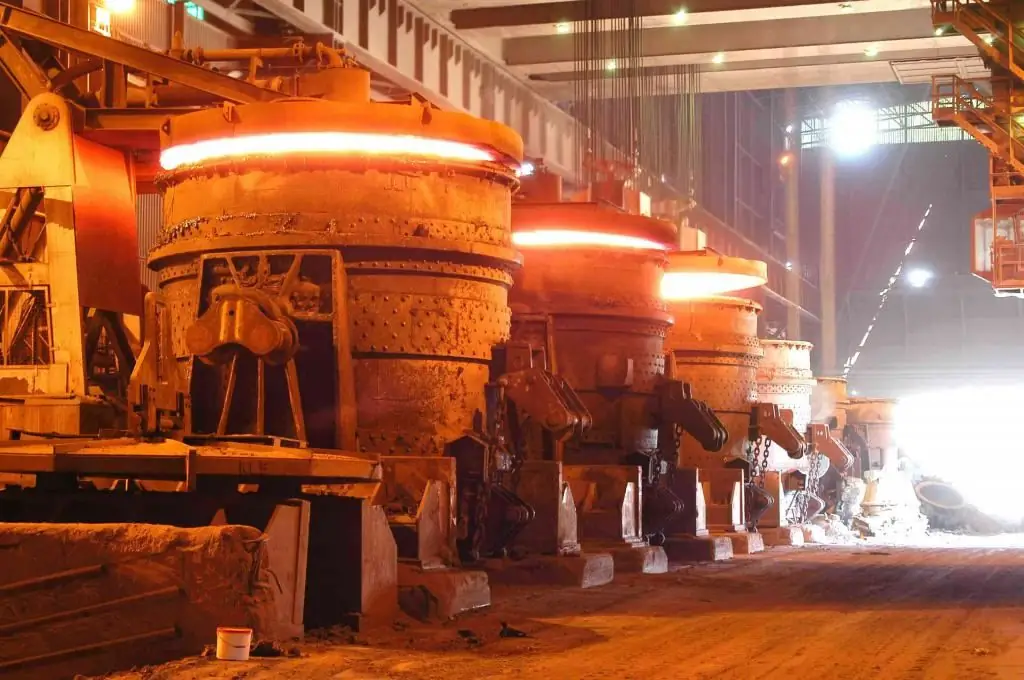
Soba seçeneklerikoniklik yok
Koni yükleme cihazı olmayan fırınlarda hammadde yüklemesi dönüşümlü olarak açılan iki adet savak bunkerinden yapılır. Hammaddeler, üzerinde belirli aralıklarla kok ve sinter bulunan eğimli bantlı konveyörlerle kendilerine ulaştırılır. Bir kısım banttan bir bunkere gelir, daha sonra döner eğimli bir tepsi boyunca fırının tepesine boş altılır. Boş altma periyodu sırasında, sabit merkezi eksen etrafında yaklaşık on tam devir yaparlar.
Yük döngüsü
Yinelenen sayıda şarj malzemesi grubu olarak adlandırmak gelenekseldir. Maksimum kısım, şarj mekanizmasının kilit haznesinin hacmi ile belirlenir. Bir döngüdeki porsiyon sayısı 5 ila 14 arasında olabilir. Yüksek fırın işleminin ürünleri tam olarak nasıl elde edilir? Bu soruyu cevaplamak için, sürecin özüne daha yakından bakalım. Karışımdaki artan karbondioksit içeriği ile düşük sıcaklık, yüksek fırında ısı değişiminin ve kimyasal işlemlerin eksiksiz olmasına katkıda bulunur. Aparatın ekonomik ve yoğun bir şekilde çalışması için, eksen boyunca ve fırının çevresindeki kantitatif karbondioksit içeriği az altılmalı ve duvarlardan bir veya iki metre yükseklikte artırılmalıdır.
Yeni fırınlarda sıcaklık kontrolü, kasadaki deliklerden problar sokularak gerçekleştirilir. Tüm işlemler için zorunlu olan, dolum seviyesinin en üstte kontrol edilmesidir.
Yenilikler arasında mikrodalga ve kızılötesi sensörlerin okumalarına dayalı temassız seviye ölçüm yöntemlerinin kullanılması yer alıyor.
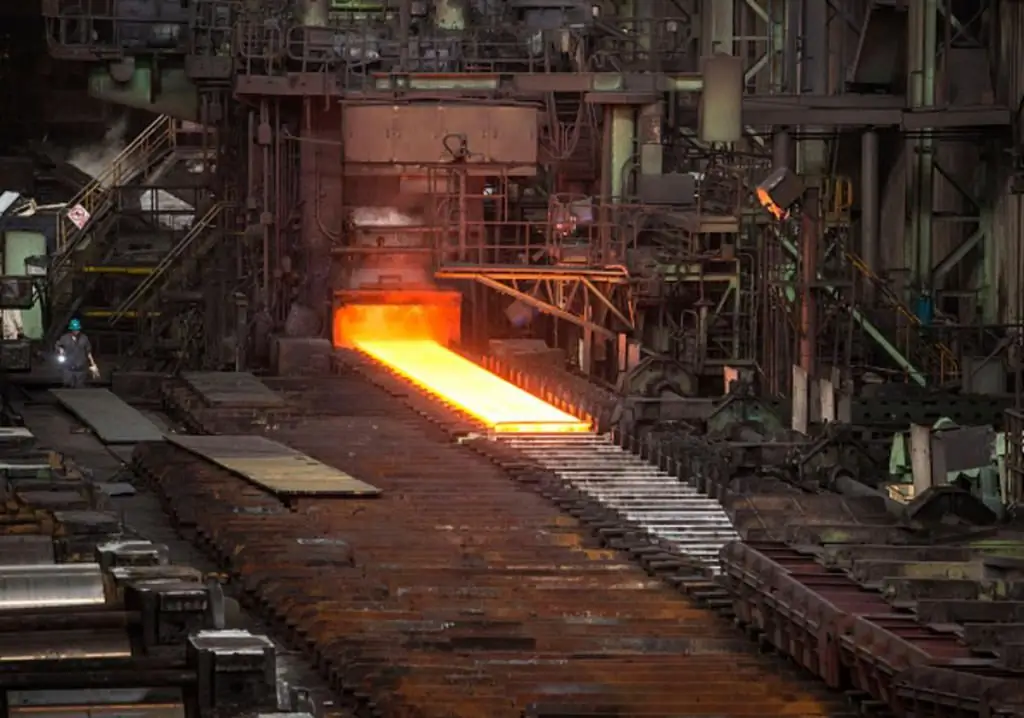
Sıcaklık dağıtım özellikleri
Isıtılmış üfleme ile ortaya çıkan ısıya ek olarak, gazların ve şarjın ısıtılması için ana ısı kaynağı olarak, geri kazanımın gerçekleştirilmesi ve ısı kayıplarının karşılanması, açığa çıkan ısı ile kayıpların telafi edilmesi mümkündür. ocağın üst kısmında yakıtın yanması sırasında. Gaz halindeki ürünler ocaktan yukarıya doğru hareket ettikçe, ısı şarj soğuk malzemelere iner ve ısı değişimi meydana gelir. Benzer bir süreç, fırın üst çıkışındaki sıcaklık düşüşünü 1400 dereceden 200 dereceye kadar açıklar.
Fazla nemi alın
Bir yüksek fırında temel fiziksel ve kimyasal süreçleri ele alalım. Yüksek fırına yüklenen şarjda higroskopik nem vardır. Örneğin, kok bileşiminde içeriği yüzde beşe kadar çıkabilir. Nem üstte hızla buharlaşır, bu nedenle onu çıkarmak için ek ısı gerekir.
Hidrat nemi, yüksek fırına kahverengi demir cevheri ve kaolin yüklendiğinde ortaya çıkar. Modern demir üretimindeki sorunu çözmek için bu cevherler pratikte hammadde olarak kullanılmamaktadır.
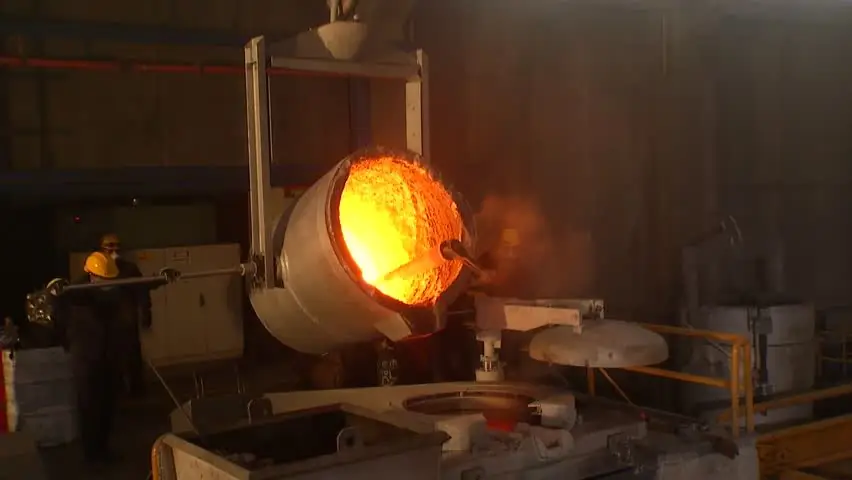
Karbonatların ayrışma süreçleri
Karbonik asit tuzları yüksek fırına girebilir. Isındıkça kalsiyum ve karbon oksitlerine ayrışırlar ve sürece yeterli miktarda enerjinin salınması eşlik eder.
Son zamanlarda, yüksek fırınlara neredeyse hiç cevher yüklenmedi. Yüksek fırın prosesinde fluxların rolü nedir? Etkinliğini arttırırlarüretim maliyetlerinin düşürülmesine olanak sağlar. Fluxed sinter kullanımı sayesinde, kireçtaşının yüksek fırın şarjından tamamen çıkarılması önemli ölçüde kok tasarrufu sağlayabilir. Aglomerasyon sırasında kireçtaşının ayrışma süreci, düşük dereceli yakıtın yanması ile sağlanır.
Demir kurtarma
Demir, yüksek fırına oksitler şeklinde verilir. Prosesin temel amacı, indirgeme yoluyla oksitlerden demirin ekstraksiyonunu maksimize etmektir. İşlemin özü oksijeni uzaklaştırmaktır, bunun için karbon, karbon monoksit, hidrojen kullanılır. Karbonla indirgemeye doğrudan süreç, gaz halindeki maddelerle reaksiyona ise dolaylı etkileşim denir. Ayırt edici özellikleri nelerdir? Doğrudan reaksiyonda, karbon tüketilir ve bunun sonucunda miktarı önemli ölçüde azalır. Demirin oksitlerden indirgenmesinin ikinci türü aşırı miktarda hidrojen gerektirir.
Süreç katı demir üretir. Dökme demirde geri kazanım derecesi %99.8'dir. Böylece sadece %0,2 -%1 cürufa dönüşür.
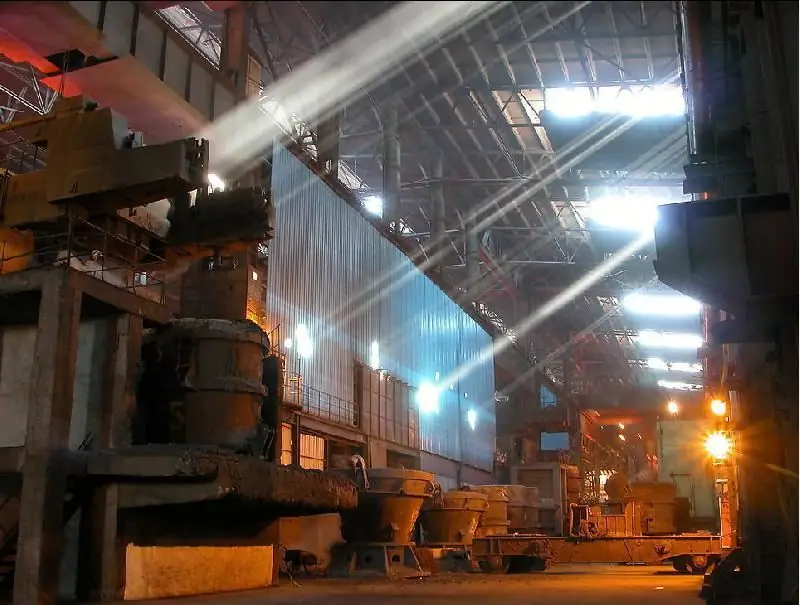
Manganlı dökme demir eritme
Yeniden üretilmiş dökme demirin eritilmesi sürecinde manganez, yüksek fırına aglomera şeklinde girer. Bazı miktarlarda manganez silikat formundaki manganez cevherleri manganezli dökme demir üretimine katkıda bulunur.
Mangan oksitlerden kurtarma adım adım gerçekleşir. İşlemin tamamlanabilmesi için fırın içerisinde yüksek sıcaklıkların ayarlanması gerekir. Pik demir eritme işlemine eşlik edermanganezin sadece %55-65 oranında az altılması. Şu anda, manganez cevherleri ve manganez kıtlığı nedeniyle, teknolojik zincirde az miktarda manganlı dökme demir kullanılmıştır. Düşük manganlı dökme demirlere geçildiğinde, metalin doğrudan indirgenmesi için tüketimi azalacağından, yalnızca manganın kendisinden değil aynı zamanda koktan da tasarruf etmek mümkündür.
Sonuç
Yüksek fırın süreci, demir ve çelik eritmenin ana yöntemlerinden biridir. İlk karışıma hangi bileşenlerin dahil edildiğine bağlı olarak, şu anda çeşitli bitmiş ürün türleri elde edilmektedir. Ortaya çıkan dökme demir ve çeliğin uygulama alanları arasında şunları ayırt ediyoruz: makine mühendisliği, kimya endüstrisi, tıp, alet yapımı.